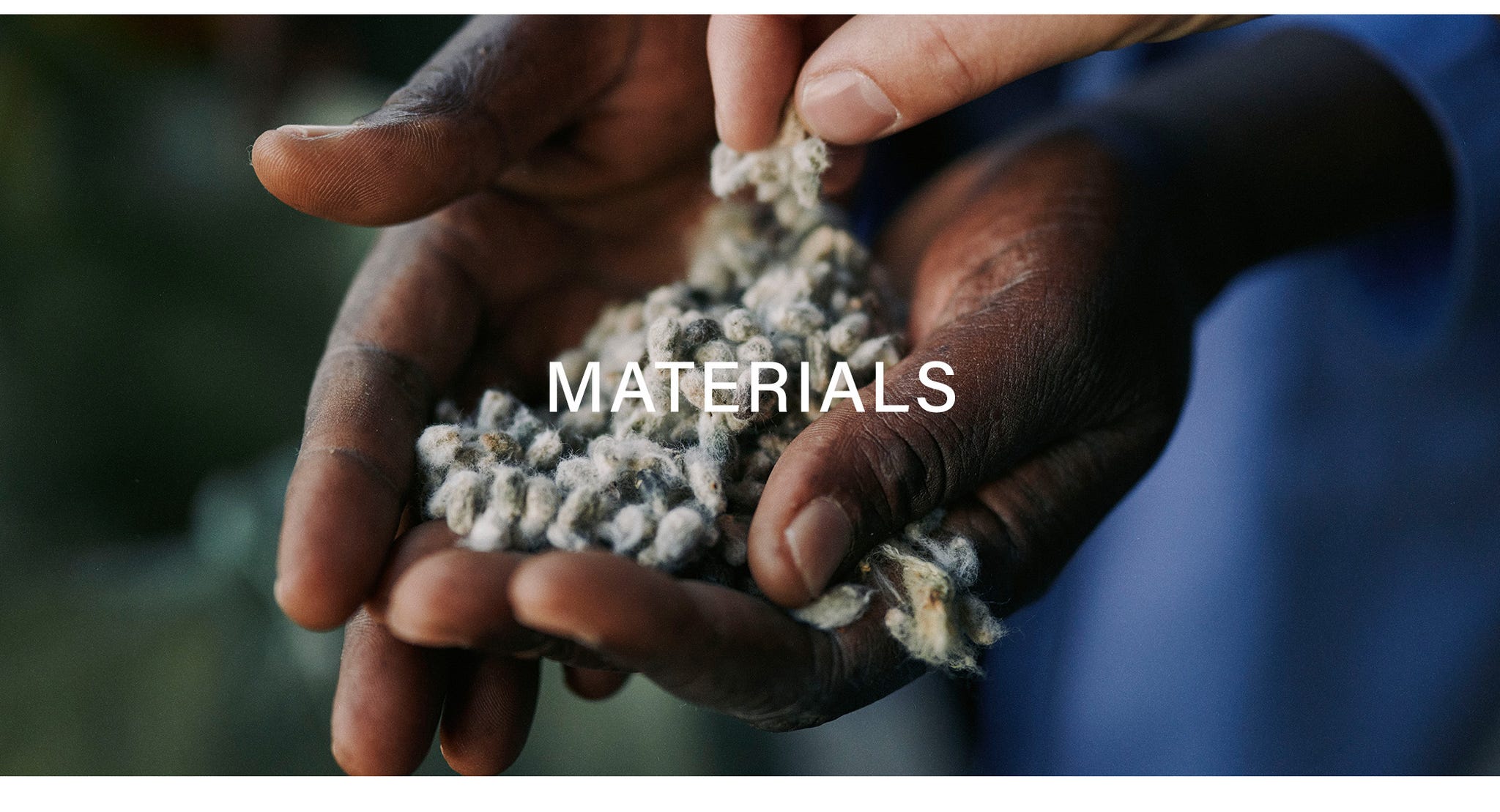
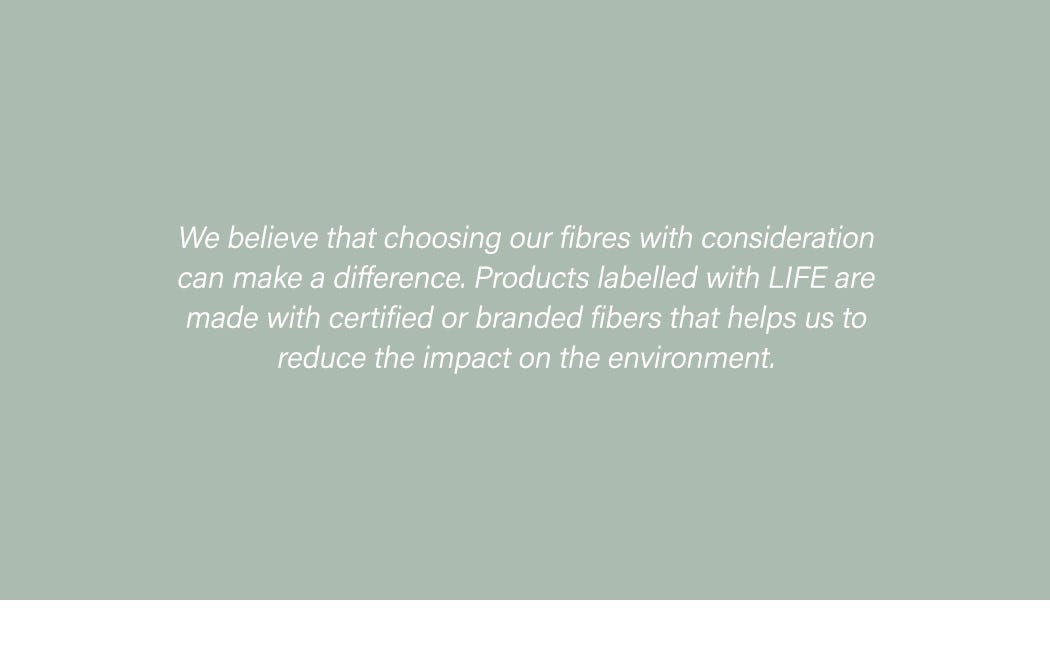
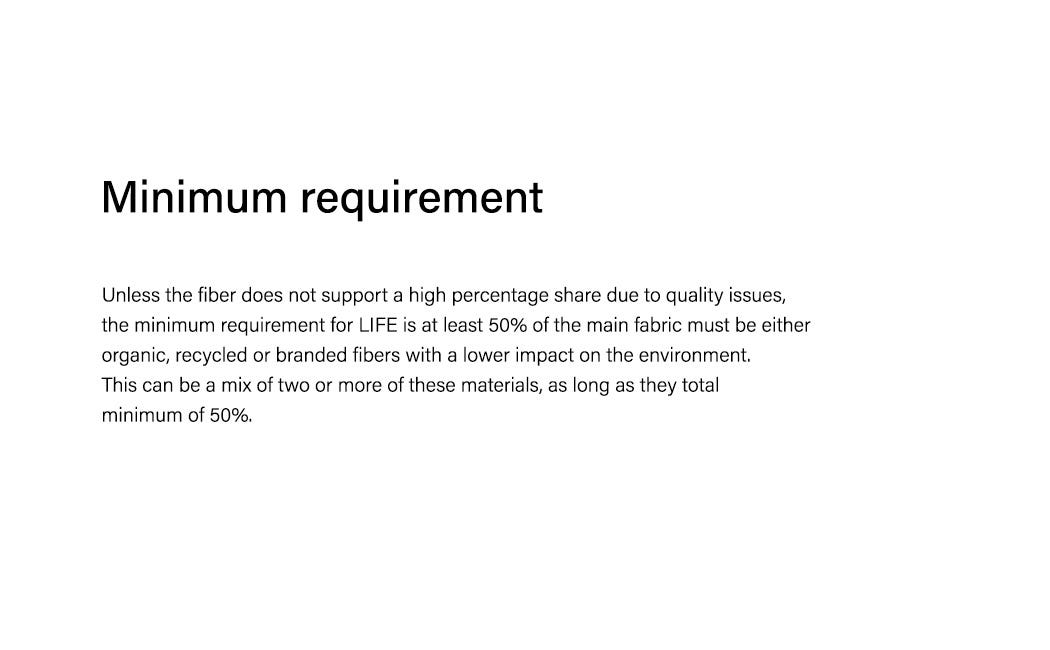
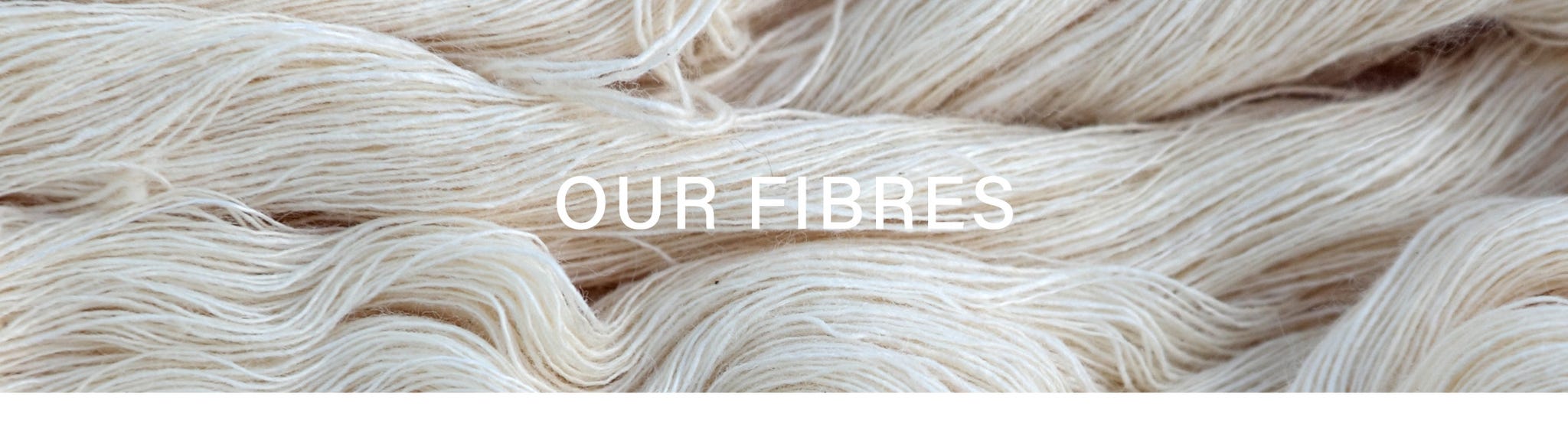

Organic cotton is grown using methods and materials that reduce negative impact on the environment without toxic pesticides or synthetic fertilizers, improving soil health and protecting biodiversity. But aside from the obvious environmental benefits of organically grown cotton, the absence of hazardous chemicals also helps to improve the work environment of the local farmer.
Cotton made in Africa, an initiative of the Aid by Trade Foundation, is one of the world’s leading standards for cotton. Their goal is to help people help themselves, via trade rather than donations, in order to improve the living and working conditions of smallholder farmers in Africa and to protect our environment. CmiA Organic cotton provides an online Tracking System to ensure complete transparency throughout the entire value chain, allowing the cotton to be traced back the entire way from the field to the finished product.
The transition period for a farmer to get the organic certification takes an average of three years, as the soil needs to recover from pesticides and synthetic fertilizers used commonly in conventional cotton farming. In this period, the farmers are not paid extra – known as the ‘organic premium’ – for their hard work and effort. Farmers growing their cotton according to the organic farming standards will save money on input cost but they also experience drop in their yield when converting their farm while working under strict regulations.

Recycled polyester is a synthetic material made from waste items like plastic bottles or leftover textiles waste from manufacturing. Recycling polyester saves natural resources and reduces the amount of waste.
Recycled nylon – also known as polyamide - is a synthetic material commonly sourced from post-industrial waste fibres like leftover fabric scraps collected from the spinning factory and waste from weaving mills. Recycling nylon fibres saves natural resources and reduces the amount of textile waste.
Recycled cotton is made from manufacturing waste like leftover fabric scraps or from used cotton garments and textiles. Recycling cotton reduces the waste of a natural resource like water. The amount of cotton waste that could have ended up in landfills is also significantly reduced.
Recycling wool saves natural resources like water and energy. Instead of shipping wool to disposal at landfills, recycling wool helps reduce the amount of textile waste. The recycled wool is reborn and later refashioned into new clothes.
CYCLO® recycled cotton is made from pre-consumer textile waste from our own supply chain. The waste is recycled into new, high-quality yarn and fibres without the use of any additional dye, water or chemicals. Saving valuable dyed cotton from going to waste and reducing the industry's environmental footprint.

LENZING™ ECOVERO™ branded viscose fibres are made from wood pulp. The wood derives from forests controlled and regulated in accordance with a stringent wood sourcing policy. LENZING™ ECOVERO™ fibres are EU Ecolabel certified, meaning that the manufacturing of LENZING™ ECOVERO™ fibres meeting high environmental standards throughout their life cycle.
Liva Reviva by Birla Cellulose is made with 80% wood pulp fibres combined with 20% pre-consumer fabric waste laying emphasis on responsible manufacturing following the principles of circular economy. Liva Reviva recycled viscose holds the distinction of RCS (Recycled Claim Standard) Certification and is traceable across the value chain.
Renewcell are pioneering a circular recycling method that creates a new, high-quality material by gently covering cotton and viscose from old clothes. Called Circulose®, this game-changing and scalable technology aims to reduce the industry’s reliance on virgin cotton and wood. Circulose® can be recycled again and again without losing any of its quality or performance value.
TENCEL™ branded modal fibres are soft, high-quality fibres made from wood pulp. The production of TENCEL™ Modal fibres is environmentally sound due to the special Eco Soft technology – a production process where wood pulp (the raw material) is produced at the same site as the fibre itself.
TENCEL™ branded lyocell fibres are high-quality, cellulose fibres made from wood pulp. The wood pulp is derived from consciously managed forestry and processed in a 99% closed-loop system where water and solvents are recycled, limiting the waste of natural resources and the use of solvents in production.